このポストにはアフィリエイトコンテンツが含まれています。
第1章:KiCadによるPCB設計データ作成とCAM出力
目次
1.1. ガーバーデータとドリルファイルの出力設定
基板をCAD設計するKiCadでは、まずPCBエディタ上で加工原点を決めます。基板外形の隅(例:左下)にドリル/配置ファイル用原点を設定し、 その位置を基準にガーバーデータを出力します。
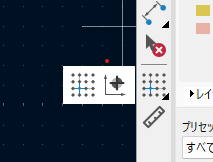
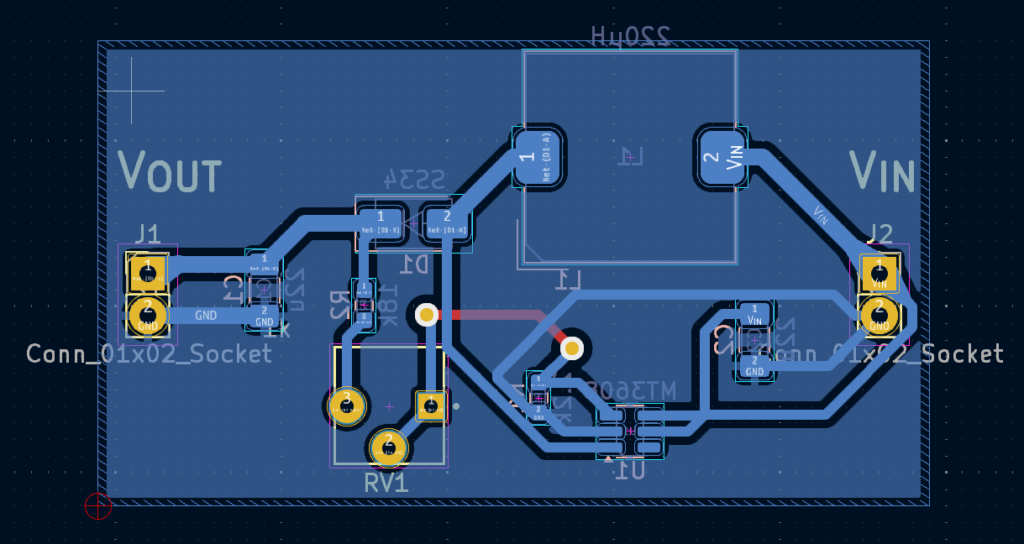
KiCadの「製造用出力」メニューからガーバーPlotダイアログを開き、必要レイヤーのみ選択しましょう。
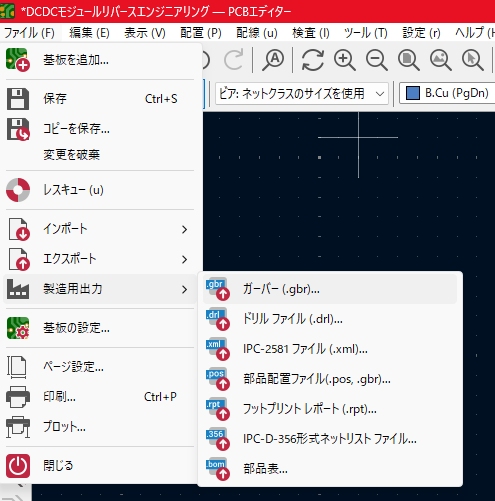
単面基板であれば銅箔面(BottomまたはFront)と外形(Edge.Cuts)にチェックを入れ、**「ドリル/配置ファイルの原点を使用」も有効にします。これにより選択レイヤーのガーバーファイル(*.gbr)が生成されます。
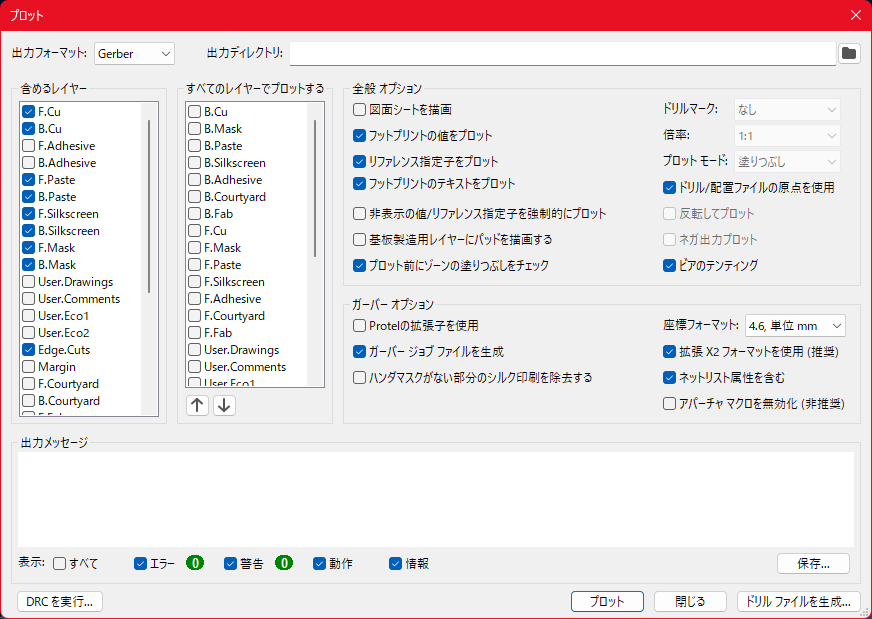
同じダイアログで「ドリルファイルを生成…」**をクリックし、Excellon形式を選択します。PTHとNPTHを一つのファイルにマージし、原点は先ほど設定した補助原点、単位はmmに設定してドリルファイル(*.drl)を出力します。これでミーリング用のガーバーデータとドリルデータが揃います。
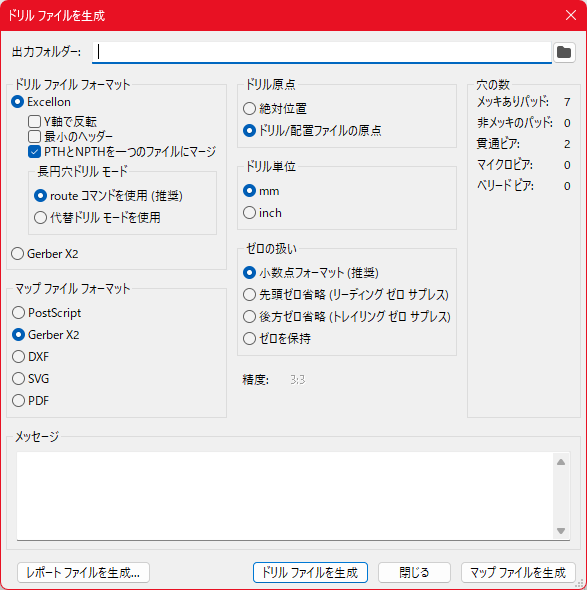
第2章:FlatCAMによるGコード生成(パターン切削・穴あけ)
2.1. ガーバー/ドリル読み込みと下準備
次にCAMソフトの FlatCAM を使用して、KiCadから得たガーバー/ドリルデータをGコード(NCプログラム)に変換します。FlatCAMを起動したら単位系をmmに設定(初回のみ)してから、先ほどのB.Cuガーバー、Edge.Cutsガーバー、ドリル.drlファイルをそれぞれ読み込みます。単面基板の場合、銅箔が裏面(B.Cu)なら図面を左右反転する必要があります。
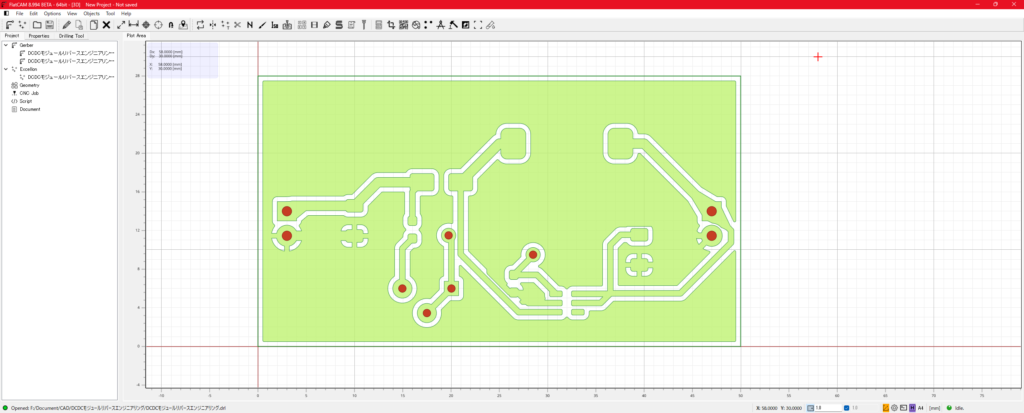
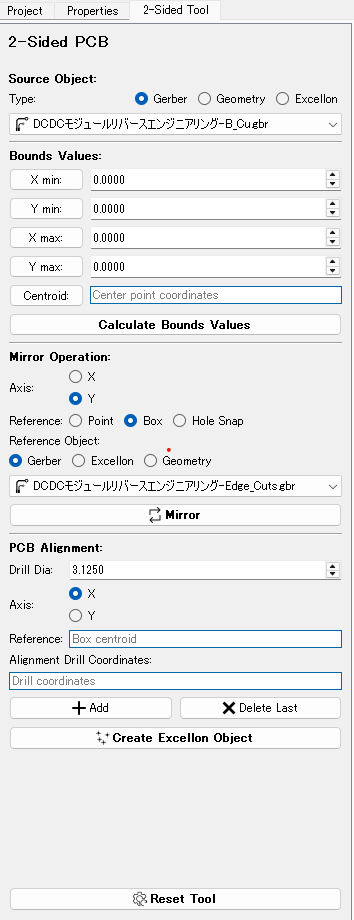
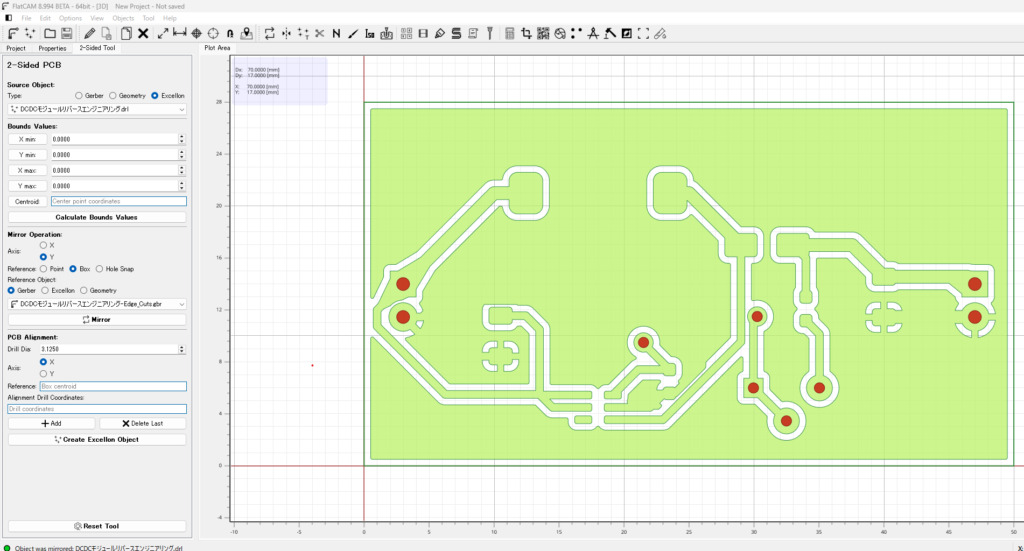
2.2. パターン切削用Gコード生成
ガーバーデータから配線パターンを削り出すIsolation(絶縁)パスを生成します。FlatCAMのプロジェクトツリーで銅箔レイヤのガーバーを選択し、ツール径(Tool dia)を先端0.138mmのV字ビットに合わせて設定します。
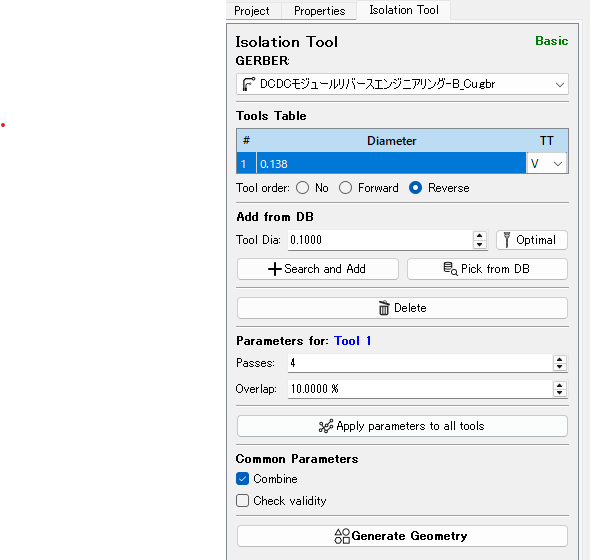
次に「Generate Geometry」をクリックして配線外形のジオメトリを生成し、さらに表示されたGeometryオブジェクトで切削パラメータを設定します。
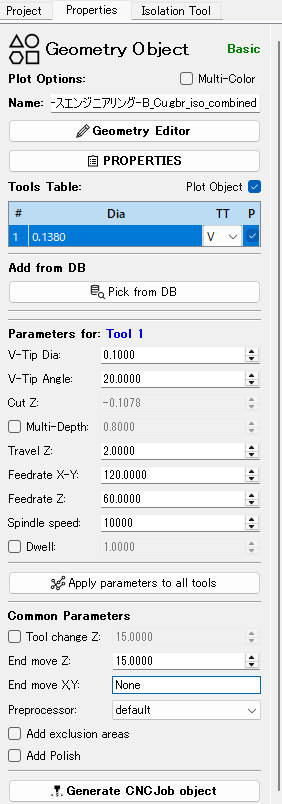
設定後「Generate」をクリックするとGコード(CNCジョブ)が生成されます.
2.3. 外形カット用Gコード生成
基板外形カット用のGコードも、Edge.CutsガーバーからGeometryを作成します。ここではFlatCAMの「Board Cutout」を使用し、Cut Zは基板厚より少し深め(例:1.8mm)、送り速度は30~50 mm/min程度にします。また基板が完全に切り離されて飛ばないよう、**タブ(ブリッジ)**となるギャップを2~4箇所設けます.
2.4. ドリルデータ(穴あけ)Gコード生成
最後にドリルファイル(Excellon)から穴あけGコードを生成します。FlatCAMで.drlを読み込んだら、通常は穴径ごとにツールを選択して「Create CNC Job」を実行します。今回は小穴のみで単一ドリル径ならそのまま全選択でOKです。
さらに、専用の超硬ドリルビットがない場合には、エンドミルを使用して任意の直径の穴をミリングすることも可能です。各工程ごとに生成されたGコードファイル(例:パターン用.nc、ドリル用.nc、外形用.nc)を用意し、CNC加工に備えます.
補足:
- KiCadから直接Gコード生成する「pcb2gcode」もありますが、FlatCAMではパターンの反転やタブ配置など細かな制御が可能。
- 複数径の穴加工ではFlatCAMの「Tool change(工具交換)」機能でM6コードによる途中停止を挿入可能。
- GRBL環境のCNC3018では自動工具交換はできないため、穴径ごとに別々のNCファイルにするか、M6コマンド対応のポーズを利用.
なお、ミリングは下記の画面で設定可能です。
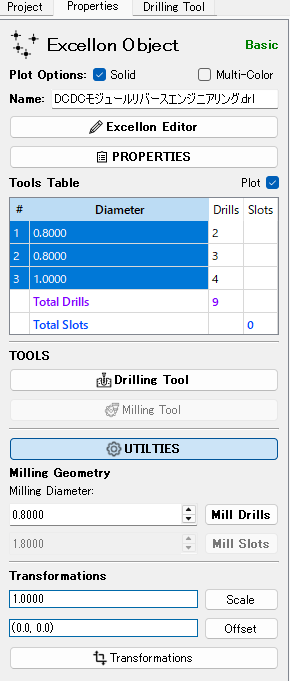
2.5. Non-copper Regionsの活用(オプション)
Non-copper Regionsは、不要な銅箔部分を除去する“クリア”機能です。
この処理は、上記のすべてのCAM手順を完了したあとに、追加オプションとして行うことを想定しています。
基板全体のGコード生成を終えた段階で、もし基板上の特定エリアを一括クリアして余分な銅を取り除きたい場合、あらためてNon-copper Regionsを設定してツールパスを追加生成し、不要な銅箔を切削します。
たとえば、広いスペースを一面にクリアしたい場合や、パターン外の銅を除去しておきたい場合に有効です。これにより最終的に意図しない銅箔が残るリスクが減り、完成後の基板外観や、後工程でのショート防止に役立ちます。
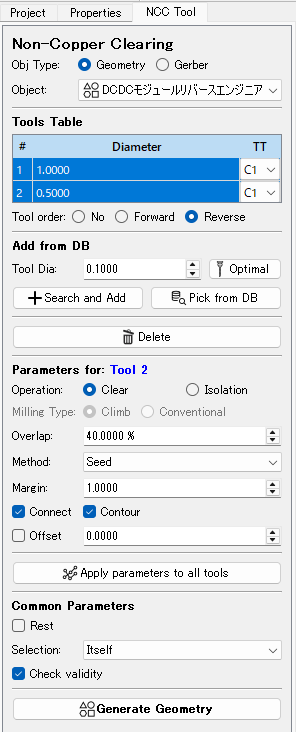
第3章:CNC3018本体とGRBL設定のポイント
3.1. スピンドルモーターの回転制御
3018標準のスピンドルモーター(775モータ)は最大24V駆動でおよそ9,000~10,000rpm程度。GRBLではPWM制御で回転数を指定し、たとえば $30=10000
と設定しておけば S10000 がフル回転指令になります。
ただし安価な3018では回転数センサーが無いので、実際の回転数はあくまで目安です。Gコード内に主軸オン(M3)と適切なS値を入れ忘れないようにしましょう.
第4章:Candleを使った加工手順と留意点
4.1. GRBLコントローラソフト「Candle」の基本
GRBL対応のGコード送信ソフトとしてCandleがよく使われます。3018付属のコントローラとUSB接続するだけで使用可能です。
- ポートを選択し接続(ステータスが “Idle” になればOK)
- ジョグ操作で軸を動かせる
4.2. 基板の固定と原点合わせ
- 基板の固定:薄い生基板は平面度確保のため両面テープ固定が手軽です。たとえば「日東 再剥離可能強力両面テープNO5000NS 25mm×20m 5000NS25」のような、しっかり固定できつつ剥がしやすいテープがあると便利です。
- Gコード読み込み:Candle上で加工用Gコードファイルを開く。
- 原点合わせ(ワークゼロ設定):
- 設計で(0,0)を基板端に設定しているなら、実機でもビットを基板端の上に合わせる
- X,Y軸を微調整し、Z軸も基板表面に刃先が触れるまで降下。手動またはZ-Probe機能でゼロ点を設定する.
4.3. Height Map(面高さ補正)の利用
PCBミリングではわずかな高さ狂いが仕上がりに影響します。CandleのHeight Map機能で、格子状に面の高さを計測・補正するのが上級者向けには必須です。
- 「Create」で測定領域とGrid数を設定
- Zt(プローブ移動時の高さ)・Zb(プローブ下限)を指定
- プロービングする点の間隔は、基板のサイズにもよりますが、5mm前後が目安です。
- 「Probe」でプロービング開始 → 「Use Heightmap」にチェックで補正を有効化
4.4. 切削実行と一時停止
- 空送りテストや「Check Mode」で安全確認
- 問題なければスピンドルON → 「Send」で切削開始
- トラブル時は「Pause」で一時停止、必要に応じてスピンドルOFF。切りくず除去などメンテナンスが可能
- 工具交換(ドリルビットや外形カット用ビット)ごとにワークゼロを再確認しながら順番にGコード実行
- 工具を交換した場合、必ずZ方向のゼロ点調整をもう一度行うこと
第5章:切削ビットの選定と加工条件
5.1. 切削ビットの種類
- V字カッター(エングレービングビット)
- 先端角20°や30°など。先端が細く微細パターン可能だが折れやすい
- 切り込み浅め(0.1~0.2mm)+ 低速送りで運用
- 先端角が大きいほど頑丈だが線幅は太め
- 小径ストレートエンドミル
- たとえば0.5mm径など。銅箔剥離にも使える
- 折れにくいが、極細ビットはやはり注意が必要
5.2. 穴あけと外形カット
- 基板用ドリルビット
- 超硬ビットで綺麗に穴あけ。
- 無ければ小径エンドミルで円形切削も可能。
- 外形カット
- 2~3mm径エンドミル推奨
- 板厚+αを数回に分けて切り込むか、低速送りで慎重に加工
5.3. 加工条件(例)
- パターン絶縁:
- 切り込み深さ0.1~0.3mm、送り100~120 mm/min
- Heightmap使用前提なら0.1mmでも可
- 穴あけ:
- ドリル径0.5~1mm、深さは貫通+0.1~0.2mm、送り40~60 mm/min
- 大きな穴を細ドリルで開ける際はさらに低速化
- 外形カット:
- 2~3mmエンドミルで厚み+0.1~0.2mm深く、送り30~50 mm/min
- タブを残して基板が落ちないよう配慮
第6章:全般的な注意とまとめ
事前シミュレーションとテスト加工を習慣化すると、上級者レベルの精密加工に近づきます。FlatCAM→NCVCやCandle上での空送りチェック、Heightmap補正の活用などで、小さなミスや機械の癖を早期に発見しましょう。
豊富な日本語ブログ記事や海外の詳細チュートリアルを参考に、CNC3018での基板内製をぜひ極めてみてください.
参考資料|References
- PICテスト用基板の製作4 KiCadでガーバーデータを作成する
- PICテスト用基板の製作4 KiCadでガーバーデータを作成する
- PICテスト用基板の製作6 FlatCAMでGコードを作成する
- KiCad + FlatCAM で KitMill 用の基板切削データを作る by uchan | elchika
- CO2レーザーカッターへの道(1) | てあそび
- Milling Printed Circuit Boards (PCBs) on a Cheap CNC Machine : 19 Steps (with Pictures) – Instructables
- Candleで生基板を切削してみる〖CNCルーターでプリント基板製作〗 – footfoot space
- 中華CNCを買って 0.65mm TSSOP 基板を作るメモ #電子工作 – Qiita
このポストにはアフィリエイトコンテンツが含まれています。